- DE
- Annual Report 2022
- www.ksb.com
BETTER THAN THE ORIGINAL
Machines in power plants, refineries or rolling mills are sometimes used for 30 years or more. But what happens if a part in one of the plant’s old motors, compressors or pumps is defective? Replacements are often difficult to obtain.
Specialised machinery manufacturers sometimes leave the market or cease production of specific parts. Operators are left with nothing but a defective component – upon which the smooth operation of an entire system may depend. This poses a difficult problem. But KSB has the solution.
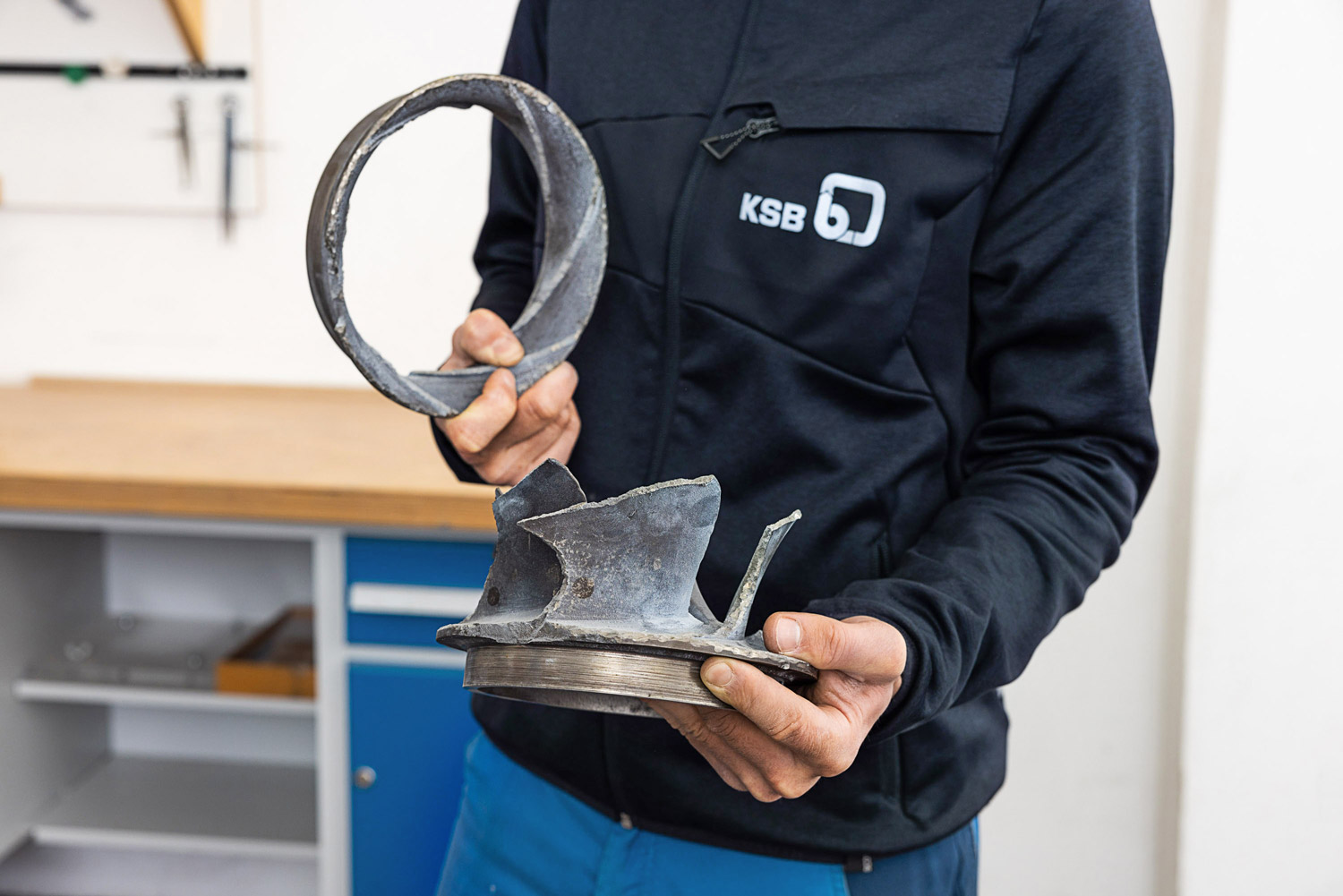
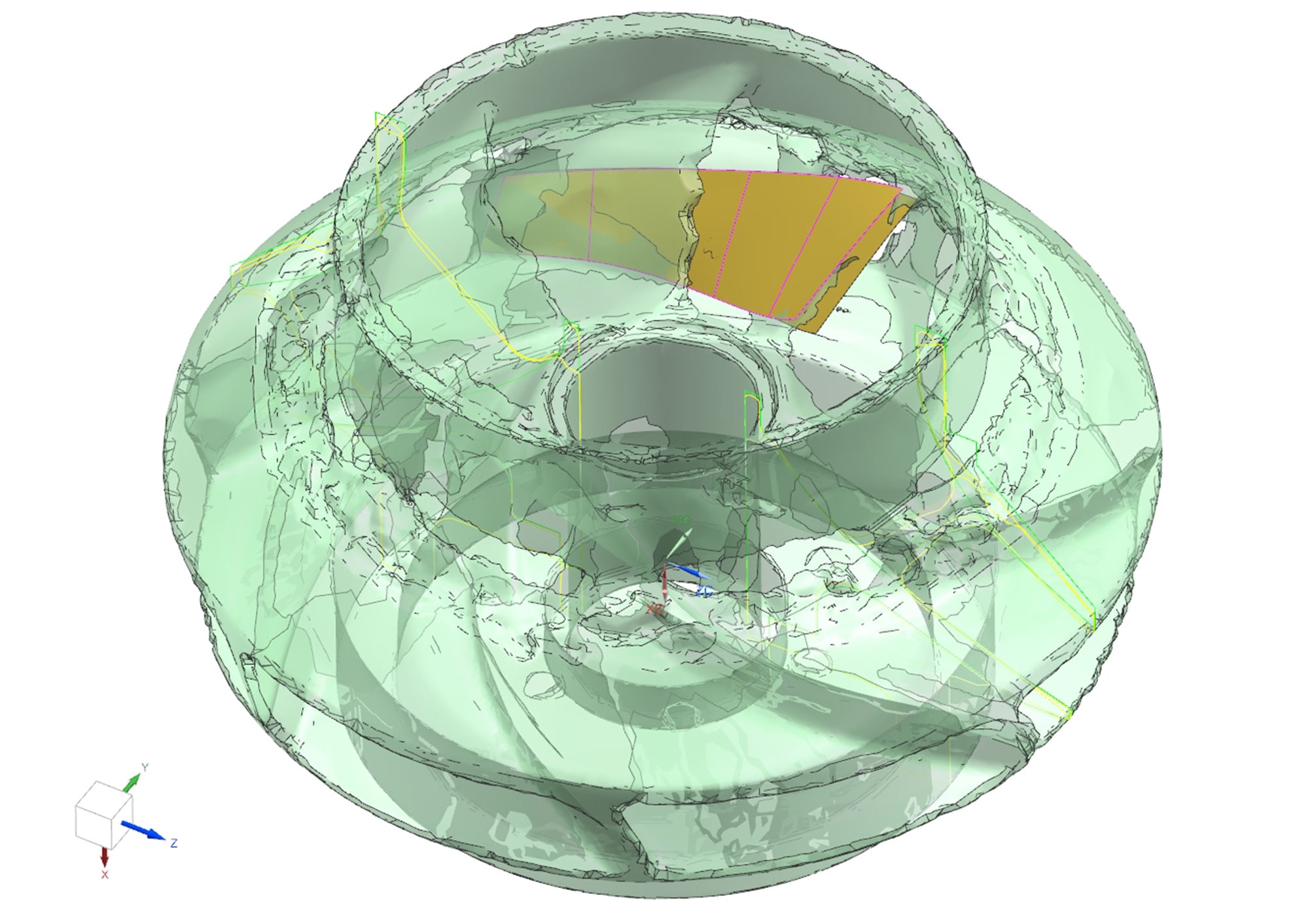
KSB creates a new component using the defective part as a template
This is where reverse engineering comes into play. The process allows KSB’s service specialists in locations including Germany, Pakistan and the USA to literally reconstruct individual components. The technology is not new. A well-known example are the activities of the Soviet design bureau Tupolev, which in the mid-1940s dismantled several huge American aircraft and rebuilt them piece by piece. However, at that time the effort required was gigantic and by no means economically reasonable.
High-performance 3D scanners
Digitalisation has dramatically reduced the work involved in reconstructing components. Today, high-performance three-dimensional scanners can be acquired for a low 5-digit euro amount. These devices can scan existing components with extremely high precision and map their contours in a so-called pixel cloud. Powerful computers then convert these into editable design files.
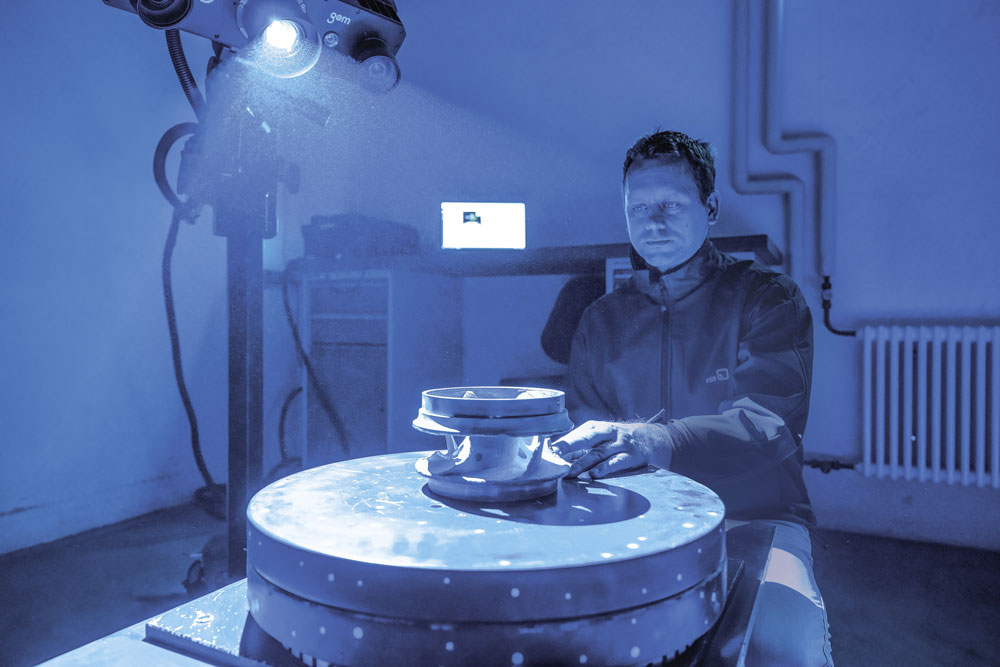
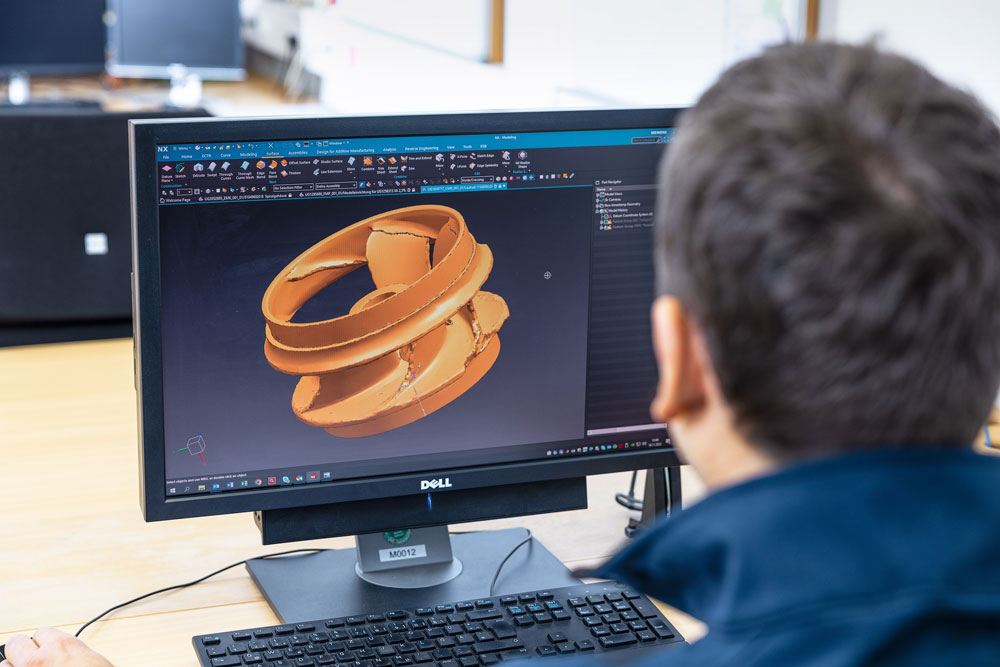
Repairing the damage digitally
The components being rebuilt are often worn or even damaged. The designer can “repair” this damage on a screen by digitally adding missing parts, corners, edges and material thickness data. This may sound simple, but it requires an enormous amount of experience and knowledge of the function and materials of the component to be made. It includes taking into account the forces transmitted to and by the component, the temperatures at which it is used, or the abrasion to which it is subjected.
Virtual design completed
Once the virtual design is complete, KSB’s reverse engineering team can optimise the component where necessary and then manufacture it. For example, developers can simulate a virtual flow through a pump impeller or casing to improve its contours in terms of strength or hydraulic characteristics. Ideally, the component subsequently manufactured offers significantly improved performance over the old part.
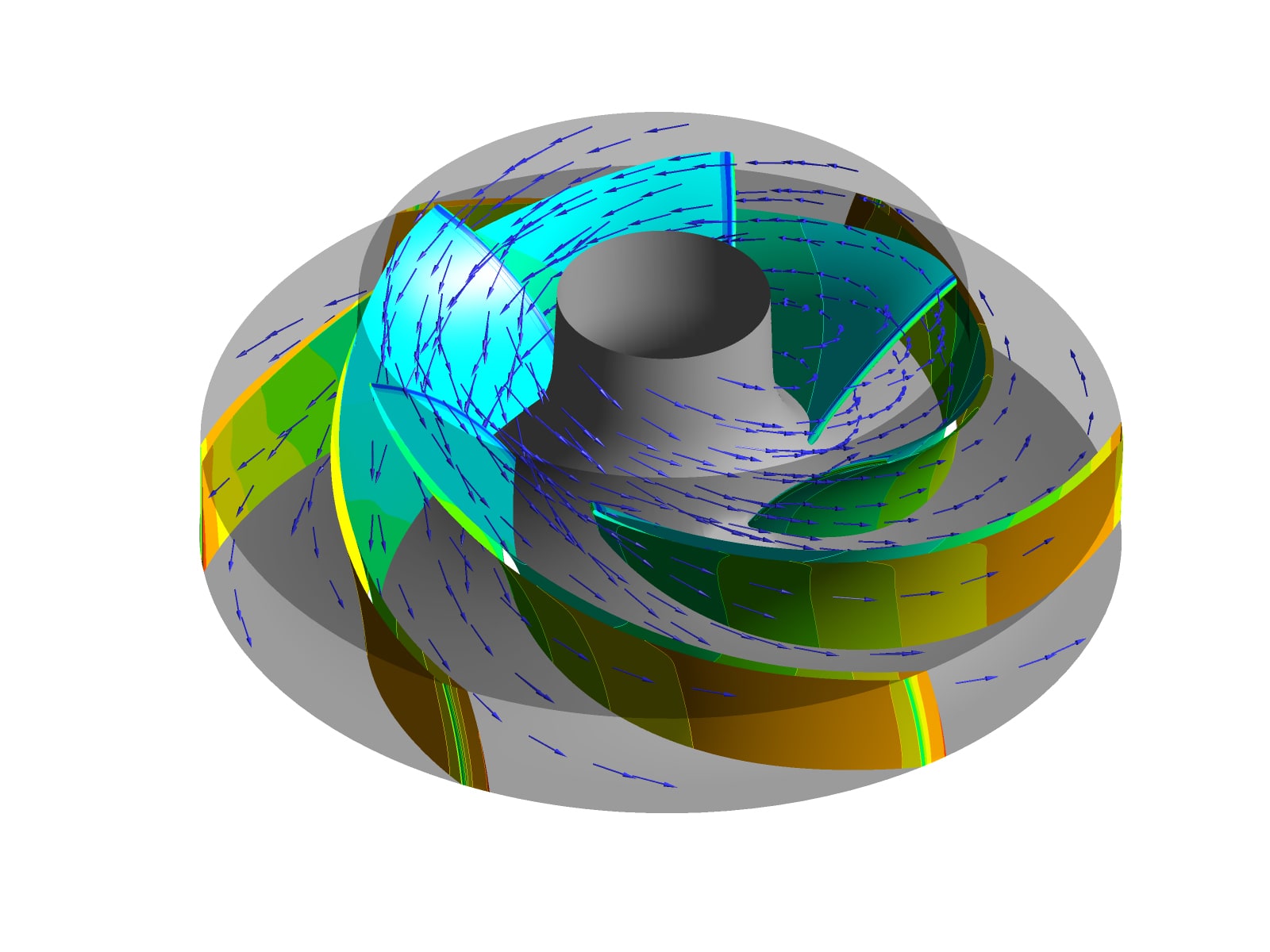
Production of the new part
After the design work is completed, production of the component can commence. KSB often uses new manufacturing processes such as additive manufacturing. This allows swift production of new components up to a certain size, depending on the print capacity of the available printer. KSB applies the so-called laser powder bed fusion process, in which a laser beam is used to build up the component layer by layer from powder. For larger components, manufacturing methods include casting techniques using computer-controlled milling machines, plastic or sand printers to produce negative moulds and patterns with core prints.
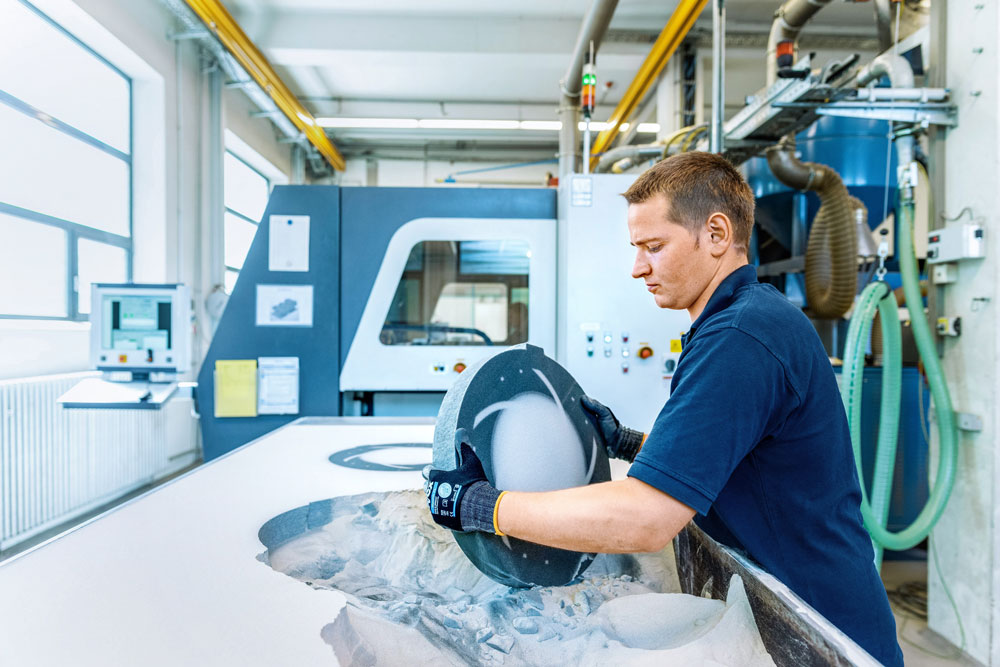
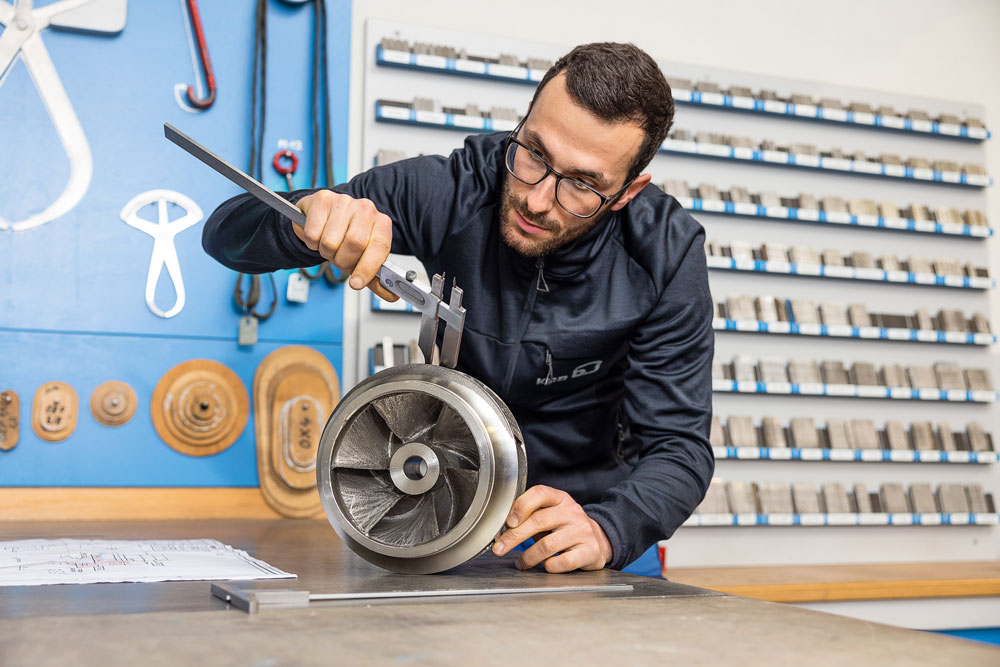
The Replacement is ready
At the end of the process, KSB’s customer receives a component that often surpasses the original in terms of quality and performance. What is more, the new component may significantly increase the service life of a pump set or system.
A video onreverse engineering by KSB