- DE
- Annual Report 2022
- www.ksb.com
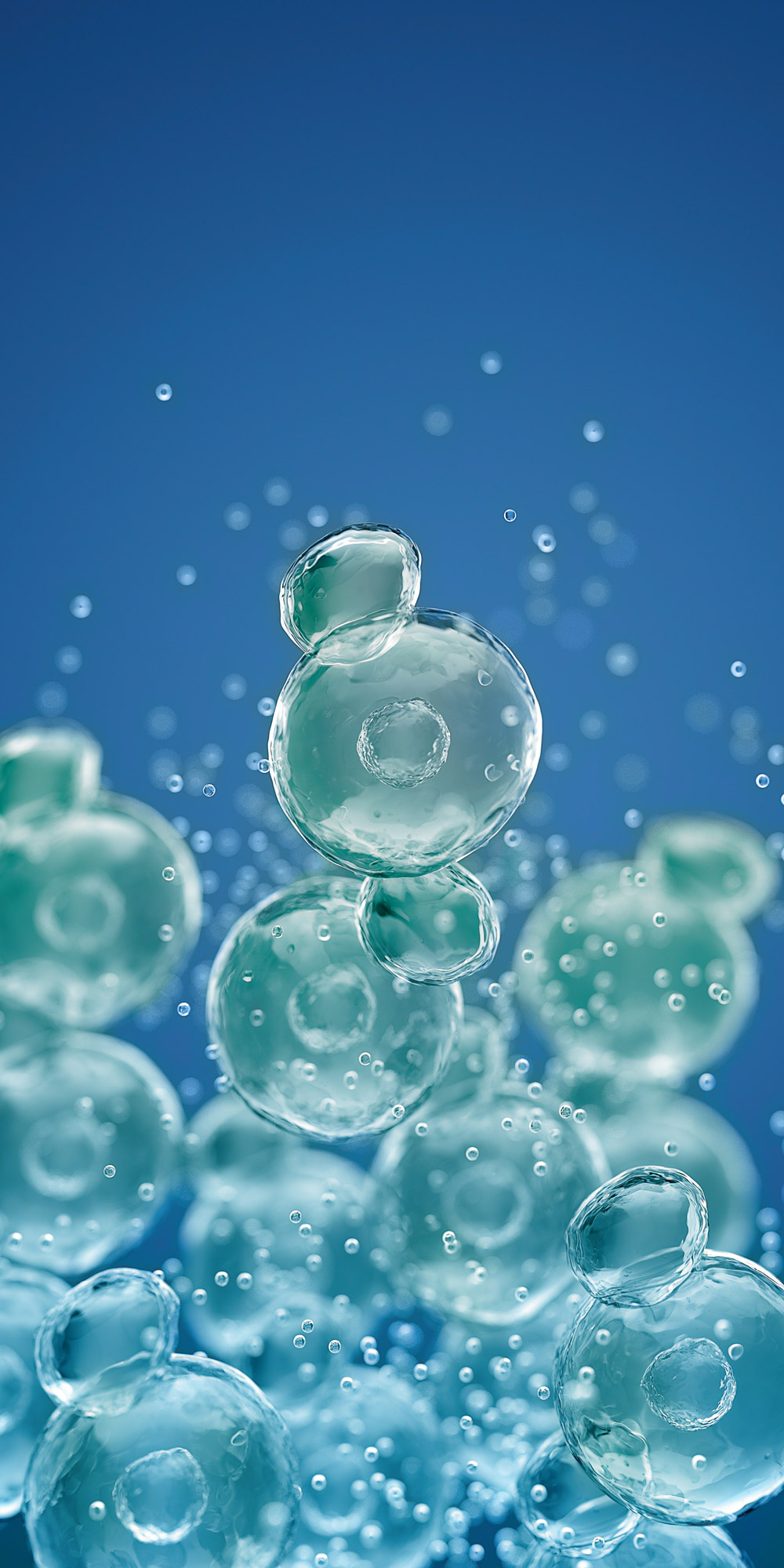
The energy Carriers of tomorrow
Today, the demands of energy-intensive sectors such as the bulk chemicals and the metal industry continue to be met with fossil fuels. In the future, these fuels will be at least partially replaced with green hydrogen. Pumps and valves promise to play a decisive role in the transition.
Almost every industrial sector recognises green hydrogen as a future energy carrier. As well as powering vehicles, it can be used to store energy generated from renewable sources. In refineries, it could replace at least part of the grey hydrogen used so far to desulphurise the precursors of petrol and diesel. The steel industry is already running pilot projects which use green hydrogen for the direct reduction of iron ore. The cement, glass and ceramics industries, too, are looking for new ways of converting their processes to deliver CO2-neutral production.
However, this transition can only succeed with the development of a hydrogen industry that is both efficient and profitable. This includes production, importing, transport and storage.
Strategic partnerships for clean energy
Green hydrogen production is most feasible when sufficient renewable energy is available for water electrolysis. The German Federal Ministry of Education and Research is therefore focusing on strategic partnerships with Southern Africa, Western Africa and Australia. These regions offer excellent conditions for producing electricity from wind and sun on unused land. In Germany, the federal government plans to establish an electrolysis capacity of at least ten gigawatts by 2030.
Fields of application focus on industry
Green hydrogen is planned to be initially used where simpler, climate-neutral alternatives remain unavailable in the foreseeable future, and where hydrogen is needed in large quantities, making economical transport more feasible. In concrete terms, this means industry first. Demand for green hydrogen is particularly strong in the chemical and steel industries.
A challenge associated with hydrogen projects is that requirements can still vary widely in terms of the components and materials used. Many questions concerning the use of pumps and valves in various hydrogen processes will ultimately only be answered when development is further advanced.
Hydrogen container
Another unresolved issue in the development of new hydrogen production systems concerns the size of the plants. Today’s electrolysers are usually modular in design. In terms of energy efficiency, it remains unclear whether individual electrolysers should be equipped with their own cooling systems, or whether several parallel electrolysers should share a common cooling unit.
Will container solutions or large plants see more demand in the future? The answer to this question directly impacts pump and valve selection. Container solutions would have flow rates of about 10 m³/h, but large plants may exceed 800 m³/h. Likewise, the operating pressure may range from 6 to 40 bar. Larger, modular facilities may also require more control systems to ensure optimum interaction between their components. Suppliers of pumps and valves will need to offer a wide product range to cover a broad field of applications. In addition, detailed knowledge of systems engineering, operating modes, materials and energy efficiency will be of crucial importance. This is especially relevant since several different technologies for green hydrogen production are available or emerging.
KSB’s products cover all of the key technologies involved in green hydrogen production including alkaline electrolysis (AEL), proton exchange membrane electrolysis (PEM) and future technologies such as anion exchange membrane electrolysis (AEM) and high-temperature electrolysis (HTEL).
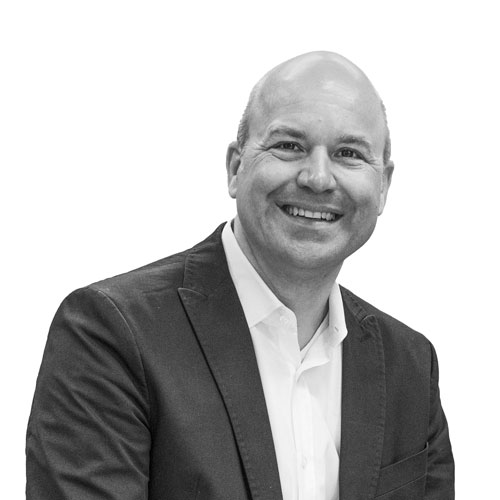
As a climate-neutral energy carrier, hydrogen could become an essential building block for replacing oil, gas and coal.
— Ulrich Stahl, hydrogen expert at KSB
The science of hydrogen
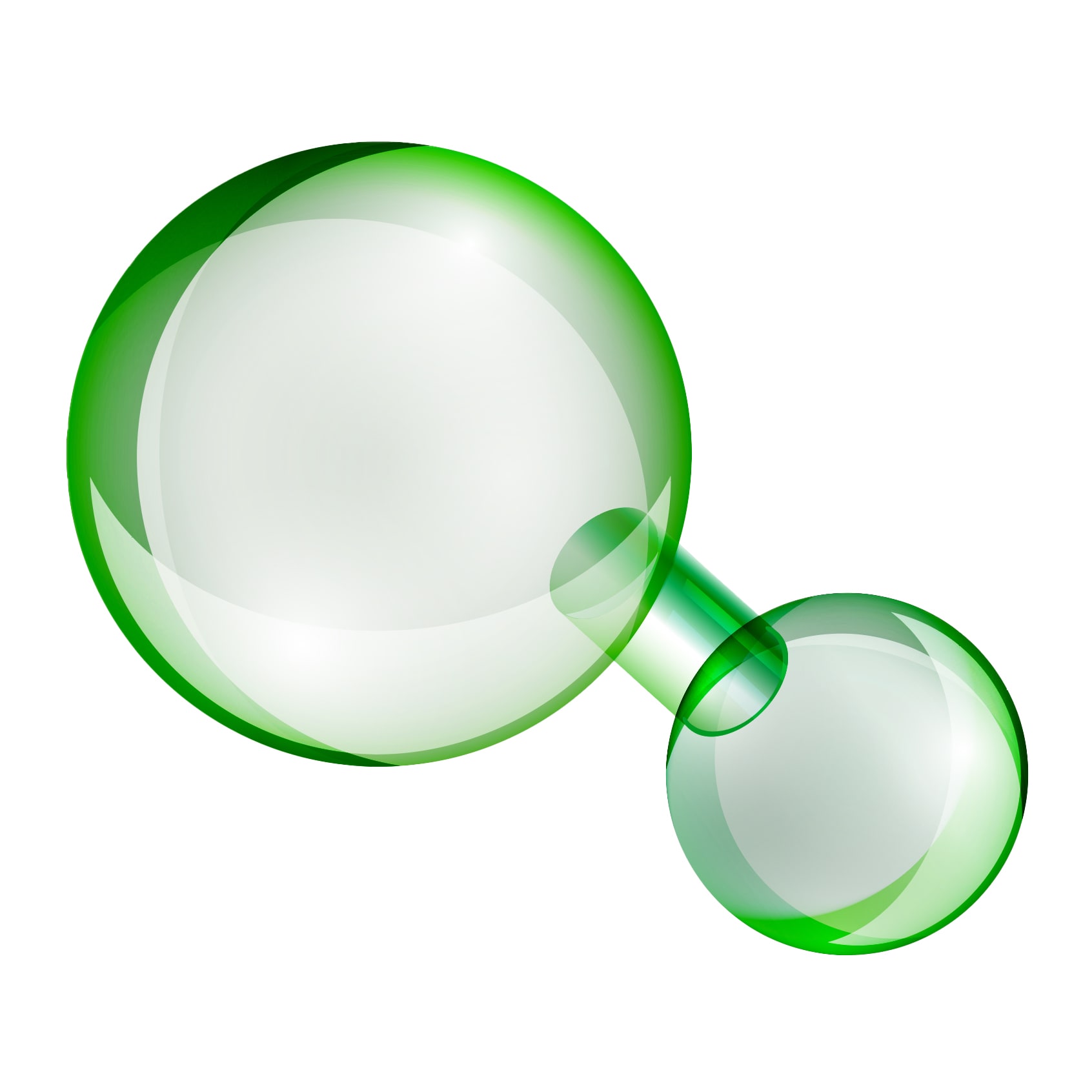
This type of hydrogen is produced via the electrolysis of water. In this process, electric current breaks down the water into hydrogen and oxygen. The electricity required for electrolysis comes exclusively from renewable energies. As a result, both the electricity used and the production of hydrogen are CO2-free.
This fuel is produced using fossil sources. For example, natural gas is converted into carbon dioxide and hydrogen. The resulting CO2 is released into the atmosphere, adding to the greenhouse effect.
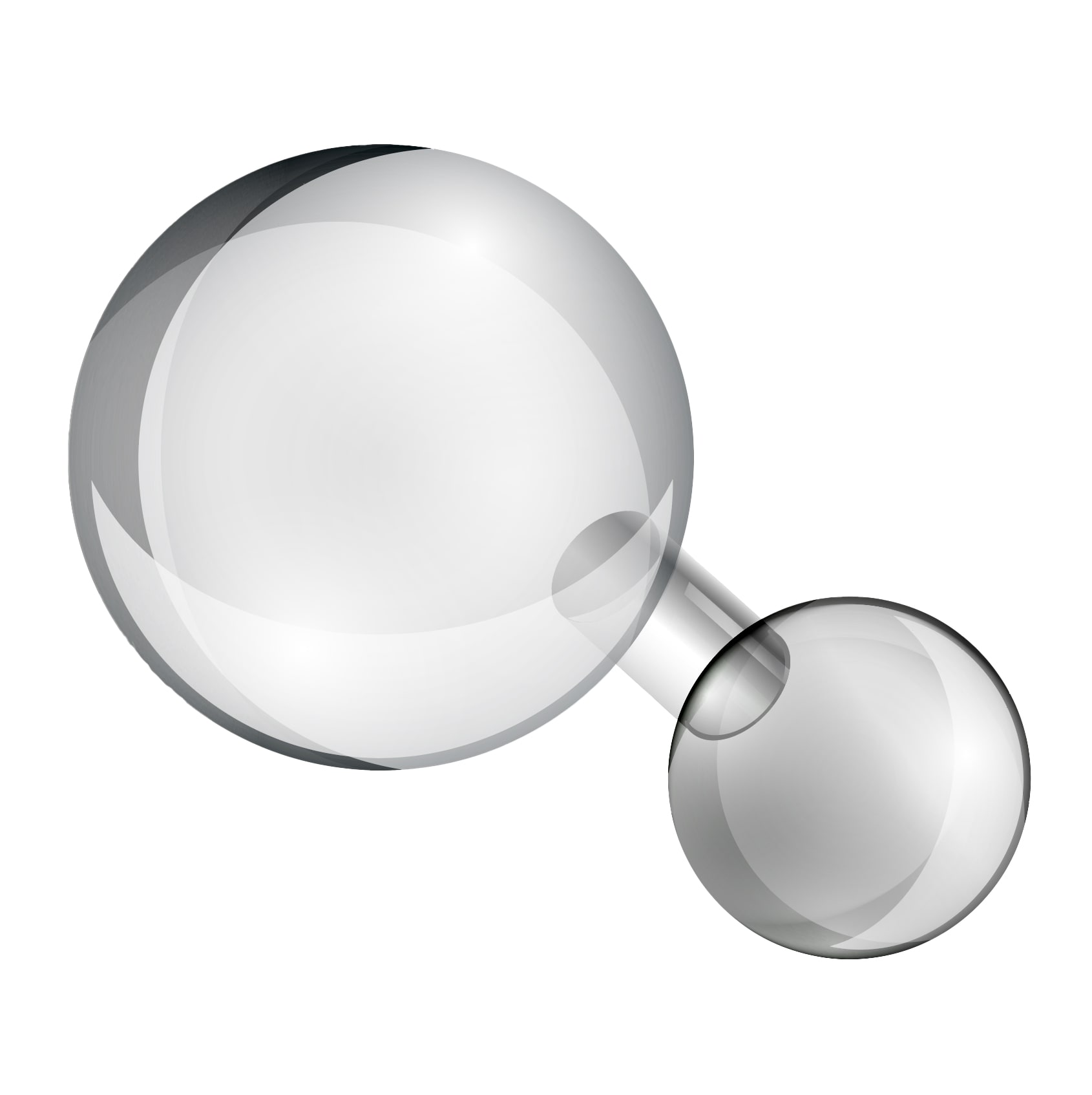
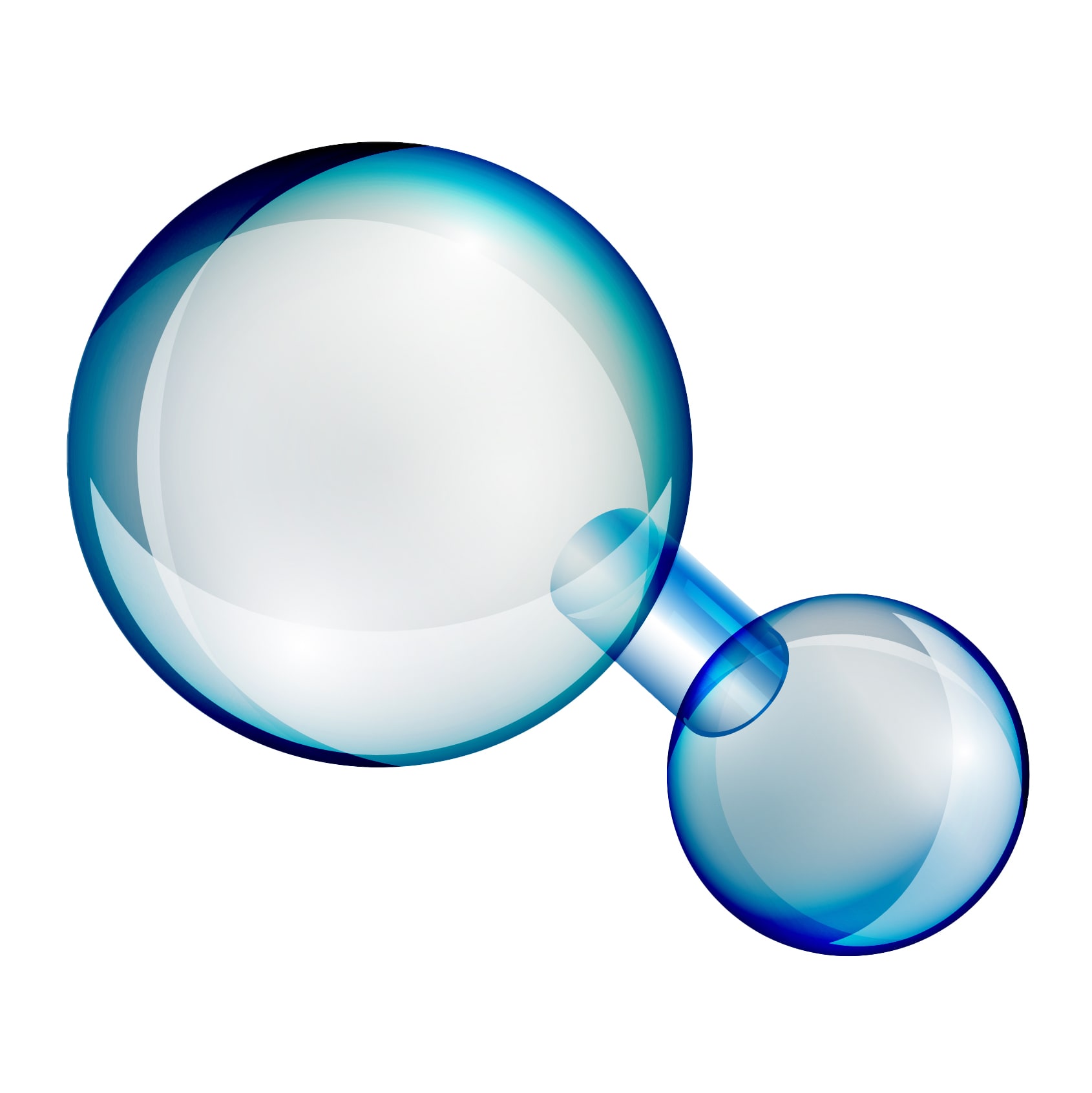
Blue hydrogen is essentially grey hydrogen. The difference: In the case of blue hydrogen, the carbon dioxide is captured and stored. This type of hydrogen production is therefore considered CO2-neutral.
This hydrogen is also produced by electrolysis. The electricity required comes from nuclear energy. Climate-critical CO2 is not produced, but radioactive waste is.
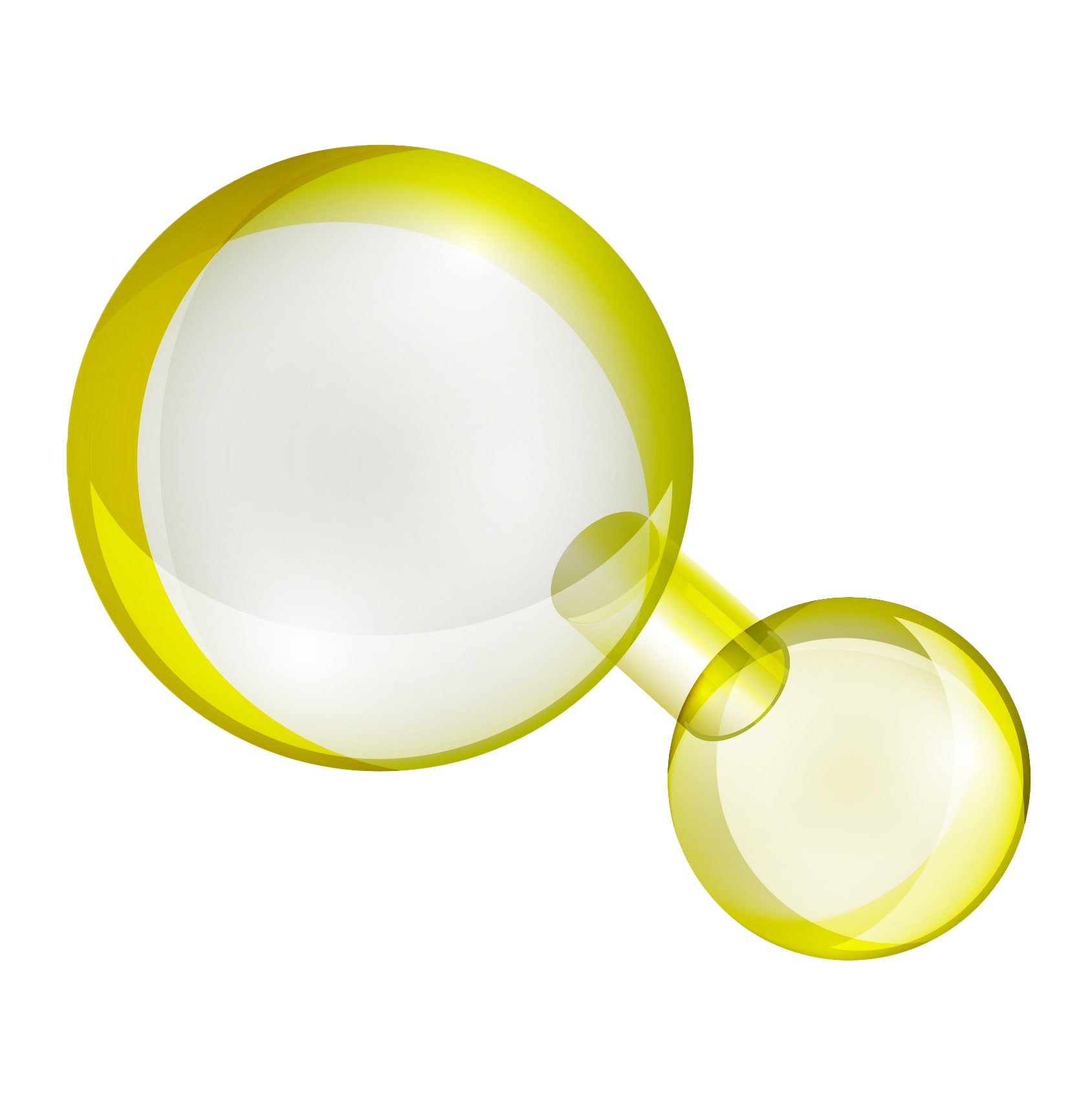
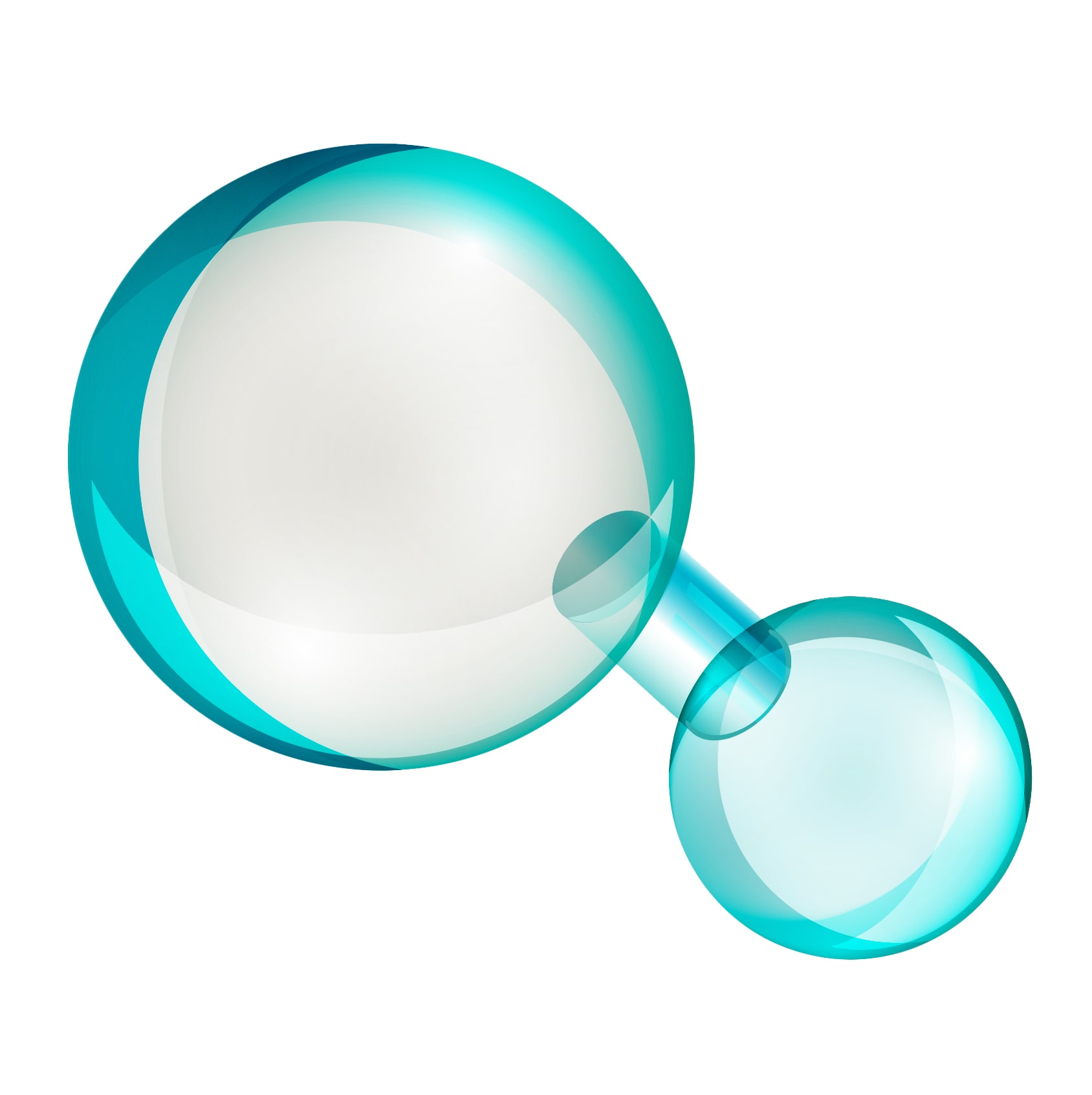
This fuel is produced via methane pyrolysis. Instead of CO2, solid carbon is formed. To make this type of production CO2-neutral, renewable energies must be used and the carbon must be permanently sequestered.
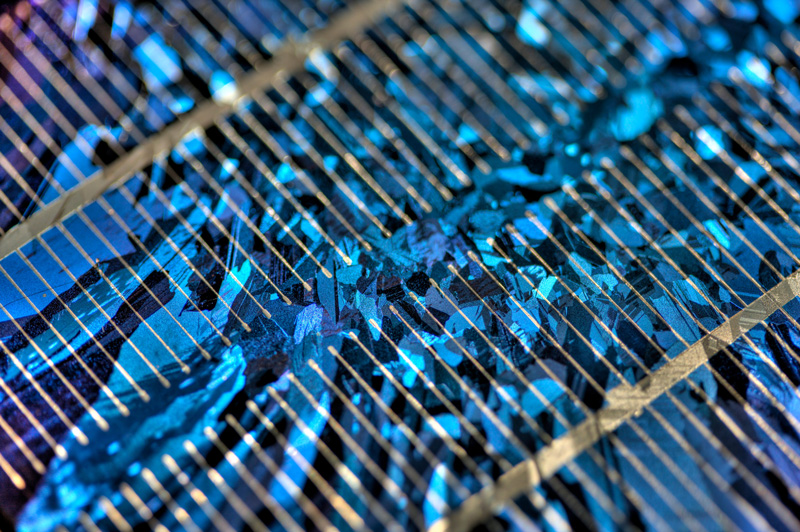
A proven technology with disadvantages
Known for more than a century, alkaline electrolysis is among the most highly developed electrolysis technologies. However, it can no longer offer much potential for reducing costs. It nevertheless remains more durable and reliable than other technologies, so its disadvantages are accepted by industry.
Innovations with potential
PEM electrolysis is a much more recent technology. Its benefits are reliability, ease of use and a high degree of flexibility. Compared with alkaline electrolysis, this technology offers considerable potential for technical developments and cost savings, and it does not require the use of any risky chemicals. Setting aside the toxic electrolyte, the application conditions for pumps and valves are similar to those of alkaline electrolysis. The new technology promises to deliver particular benefits once hydrogen production from renewable energy sources becomes widespread in future.
KSB is also equipped for future technologies such as anion exchange membrane electrolysis (AEM) and high-temperature electrolysis (HTEL). Here, the challenge is dealing with high temperatures that place exacting demands on materials.