- DE
- Annual Report 2022
- www.ksb.com
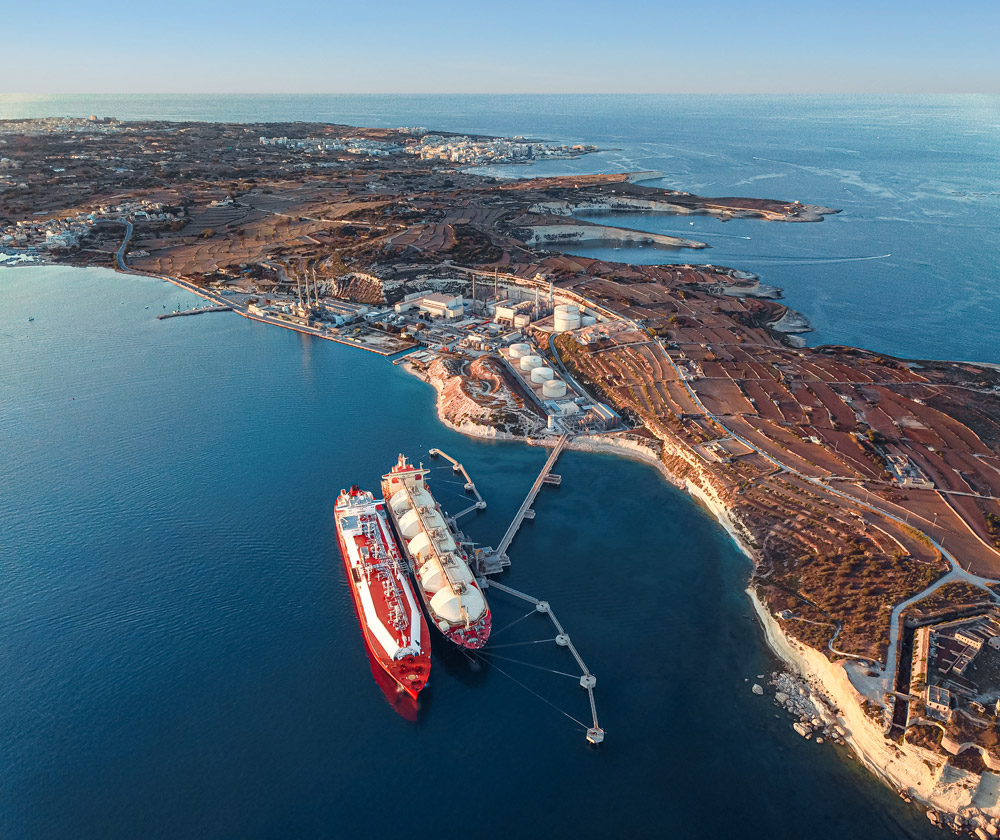
Keep things
Liquefied natural gas infrastructure is expanding worldwide. It involves highly complex systems posing enormous technical challenges. KSB has the right products for the task.
A large proportion of natural gas is liquefied prior to transport. Transforming gas into liquid form means cooling it to below –164 °C. Liquefied natural gas (LNG) is reduced in volume by a factor of 600, facilitating transport and storage. This means that the largest tankers can ship almost 150,000 cubic metres of liquefied gas.
Extreme conditions
LNG’s cryogenic temperatures leave most metals brittle with reduced strength. Special low-temperature materials are therefore required for mechanical components and sealing to ensure safe, reliable and long-term operation. KSB thus tests its valves for liquefied gas with liquid nitrogen at temperatures of –196 degrees Celsius at the company’s French factory in La Roche-Chalais. Valves in LNG systems also have to withstand enormous pressures of up to 100 bar which severely test their integrity.
Use on specialised ships
However, highly complex components such as valves are not only found on liquefied gas tankers. LNG logistics requires increasing numbers of specialised vessels to meet the surge in demand on the world market.
Today, the purification and liquefaction of natural gas usually takes place on land. In the future, offshore solutions will also be used for natural gas fields located far out at sea. These so-called FPSO (Floating Production Storage and Offloading) tankers are capable of extracting, purifying, storing and offloading natural gas. Elaborate infrastructure involving deep-sea pipelines is not necessary.
Floating storage and regasification units (FSRU) are another type of specialised vessel. These can be moored in a port for a short time to land, store and regasify LNG.
Natural gas on the move
1
Before an LNG tanker sets off on its long journey, the natural gas is purified and transformed into a liquid state via a complex liquefaction line which performs cooling in several stages.
2
At the destination port, the vessel offloads the liquefied natural gas at a landing terminal. The LNG is transported onshore from the insulated spherical or membrane tanks via specialised equipment with the help of on-board pumps.
3
Still in the cryogenic state, the natural gas awaits further processing in giant insulated tanks. It is temporarily stored under atmospheric pressure until further transport or regasification.
4
Regasification plants heat the deep-cooled natural gas and convert it back into the gaseous state. In the process, its volume expands 600-fold.
5
Finally, the gas can be fed into the transmission grid. This transports it to consumers in commercial enterprise and private households.
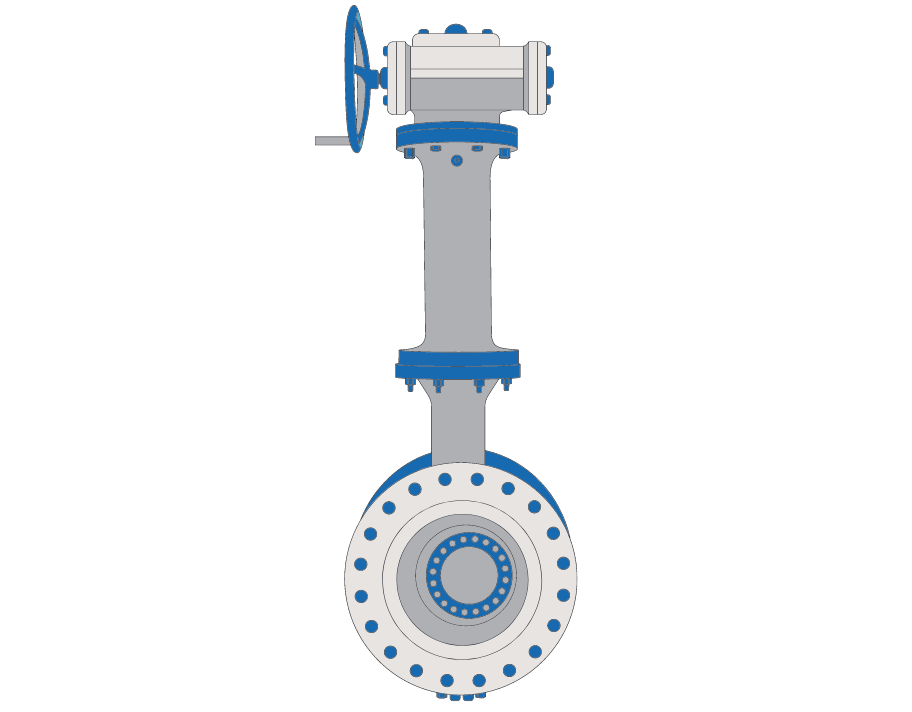
Cryogenic valves from France
High-performance TRIODIS valves are mainly used in natural gas liquefaction, regasification and transport. Their strength: reliable and absolutely leak-tight operation. The maintenance-free cryogenic valves are engineered to withstand operating pressures of up to 100 bar. A special design allows them to be operated by smaller actuators. TRIODIS is available in diameters from 20 centimetres to 1.20 metres.

Control valves from India
KSB supplies various straight-way and angle control valves for the LNG market including MIL 21000, MIL 41000 and MIL 50000 via its Indian subsidiary, KSB MIL Controls Limited. They are ideal for controlling the flow of cryogenic fluids such as liquefied natural gas. The valves can handle the toughest conditions.
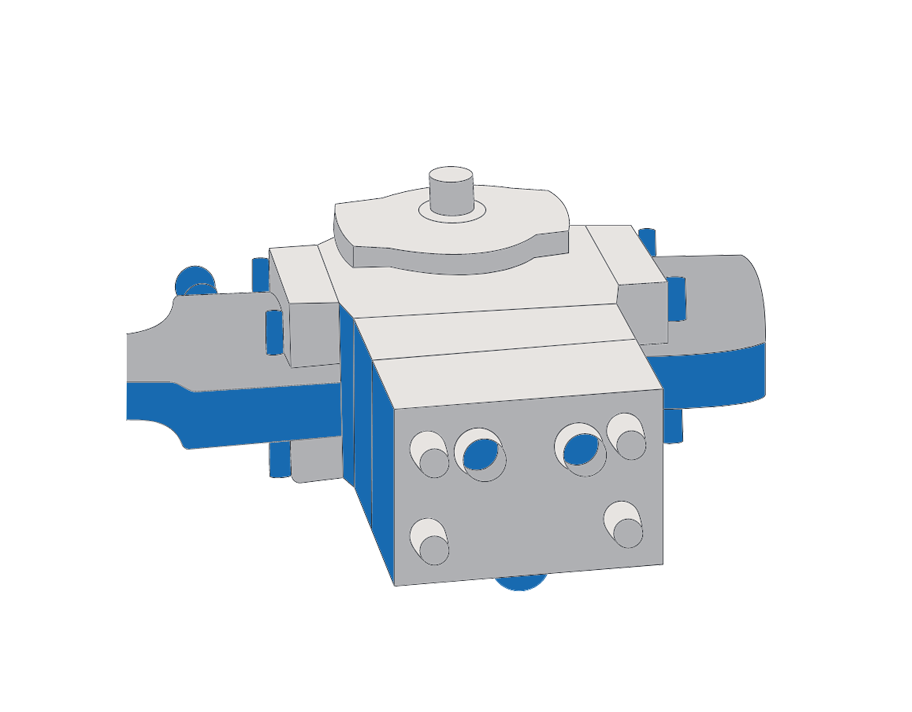
Actuators from South Korea
The HQ series from the South Korean manufacturer KSB Seil Co., Ltd. are hydraulic actuators for mounting on quarter-turn valves. They can be used to actuate butterfly valves and ball valves, for example when loading or offloading an LNG tanker at a terminal. The compact actuators are floodable and seawater-resistant – ideal for use on the world’s oceans.